In the home textile industry, quality management is not just about meeting customer expectations—it’s the foundation for building trust and a lasting brand reputation. As an experienced textile manufacturer, Mefiss understands the critical importance of strict quality control at every stage of production. Here, we share 10 essential points that outline how a home textile factory ensures consistent product quality, based on our own approach.
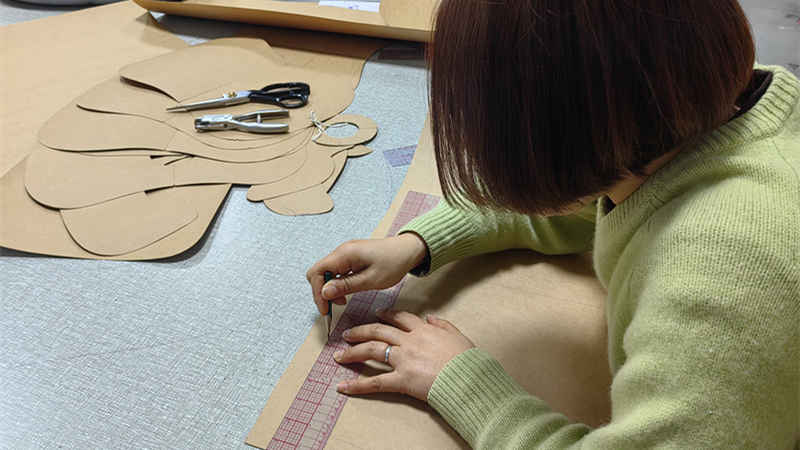
1. Strict Raw Material Control
Quality management begins with the selection and inspection of raw materials. High-quality home textiles come from superior raw materials. At Mefiss, we implement a rigorous warehouse inspection system, where every batch of materials is either fully inspected or randomly sampled before use to ensure compliance with national and industry standards. High-quality raw materials are the foundation for premium finished products.
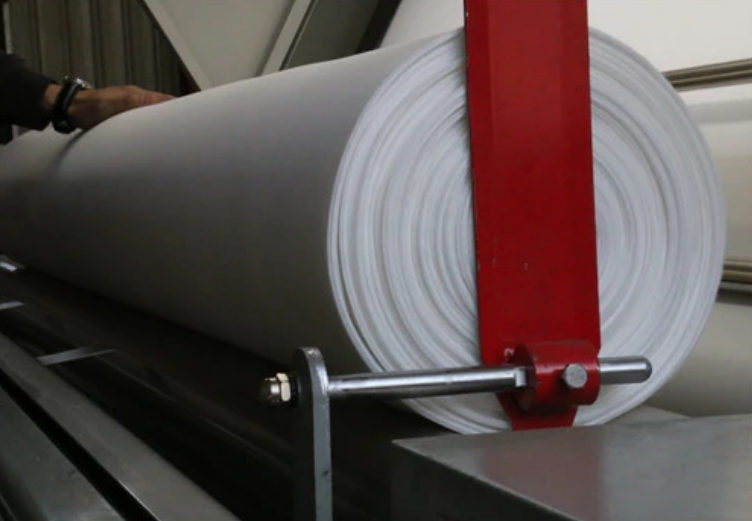
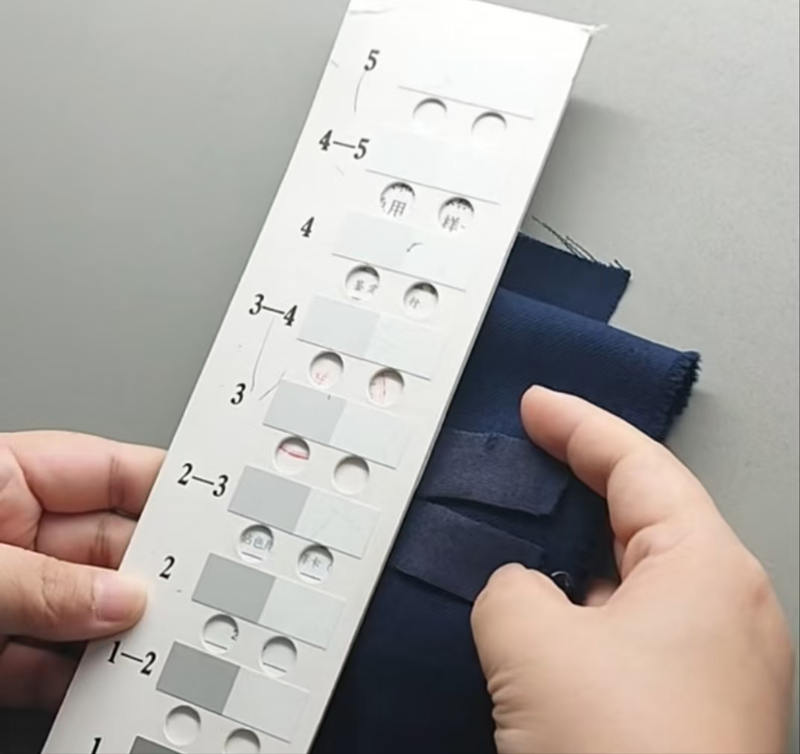
2. Long-Term Supplier Partnerships and Quality Evaluation
Building long-term, trusted relationships with suppliers is key to ensuring stable material quality. At Mefiss, we work with suppliers we've trusted for years, conducting annual quality evaluations and providing feedback for improvements. These long-term partnerships reduce procurement risks and offer a higher level of quality assurance for the materials we use.
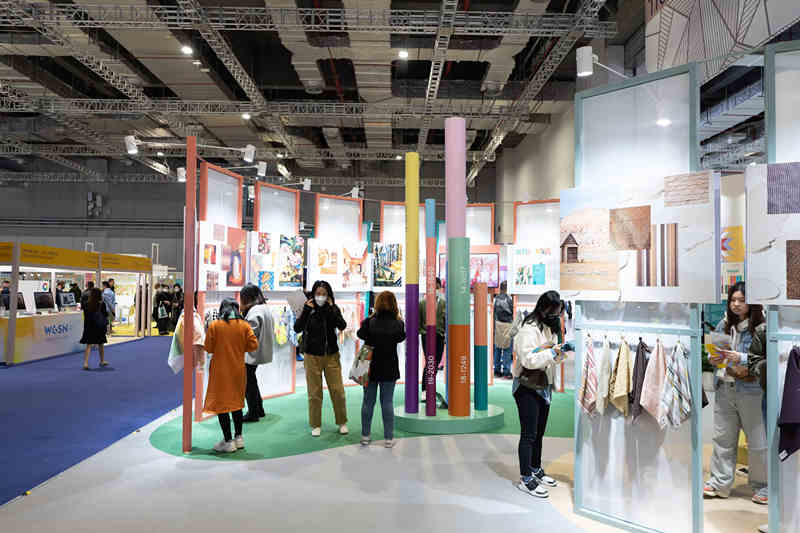
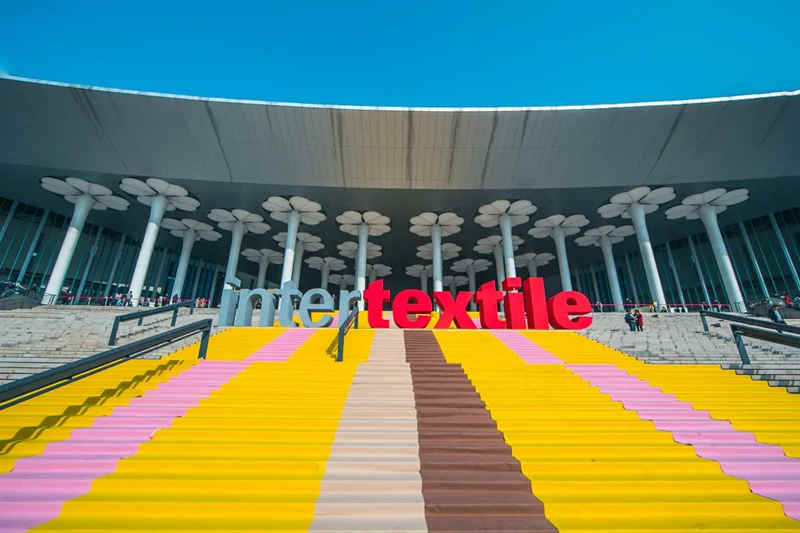
3. Third-Party Testing for Compliance
Before mass production, both raw materials and finished products must pass testing by reputable third-party agencies. Mefiss partners with SGS and TUV to ensure compliance with international standards on heavy metals, formaldehyde, azo dyes, pH values, pilling, shrinkage, color fastness, and tear strength. This step is crucial for maintaining global market quality standards.
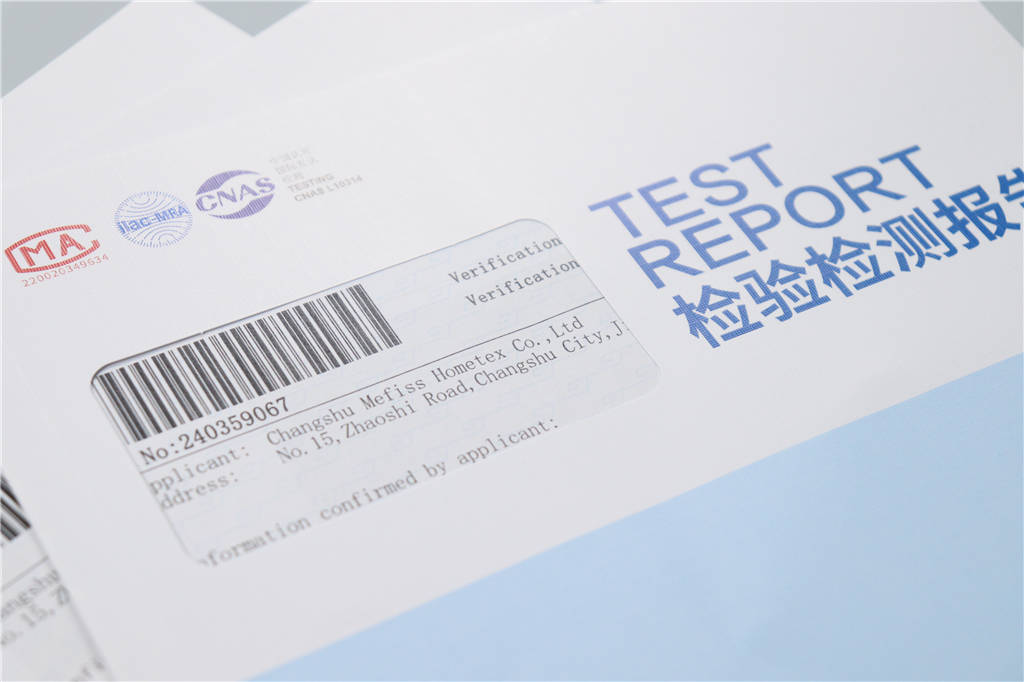
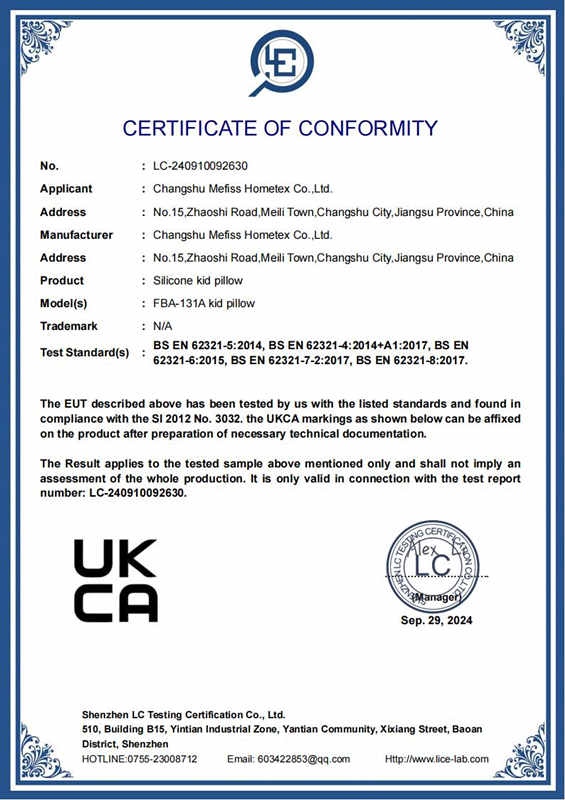
4. Comprehensive Production Process Documentation
From raw materials to finished goods, every product is supported by a detailed production process file. At Mefiss, we create standardized process documents that record material specifications, quantities, sizes, and usage details. During bulk production, each worker follows a detailed process sheet, minimizing errors and ensuring consistency across production.
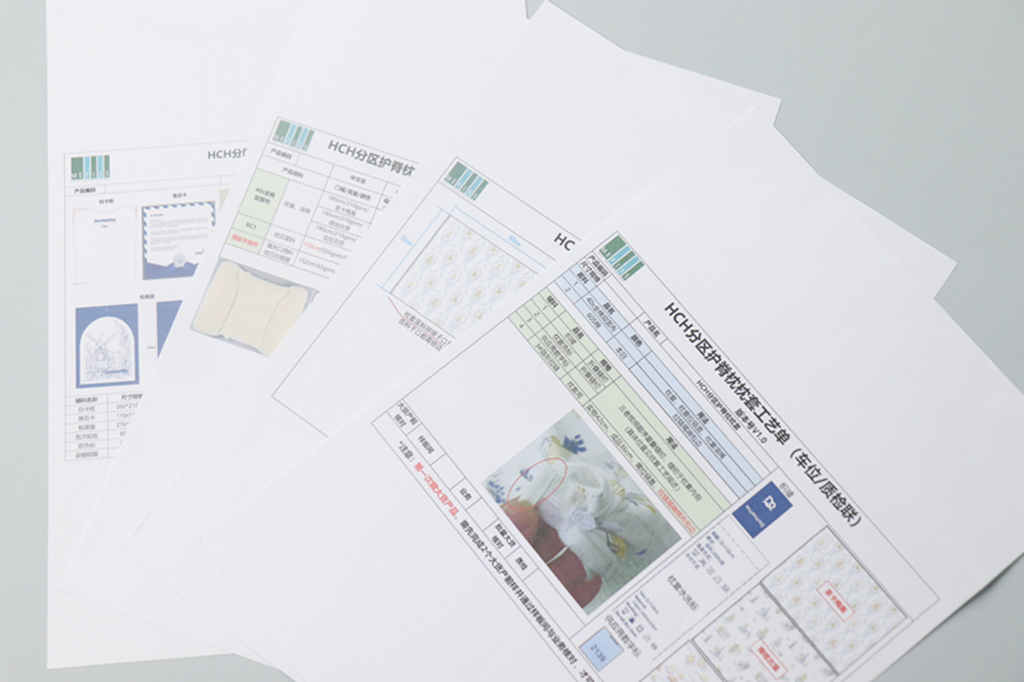
5. Pre-Production Sample Confirmation and Meetings
A confirmed sample is critical for guiding mass production. At Mefiss, our sample room produces the final approved sample before production begins. We also hold pre-production meetings, where the sales, production, and quality teams come together to thoroughly discuss the customer’s quality standards, product usage, size tolerances, packaging, and delivery expectations. This cross-team communication helps avoid misunderstandings during production.
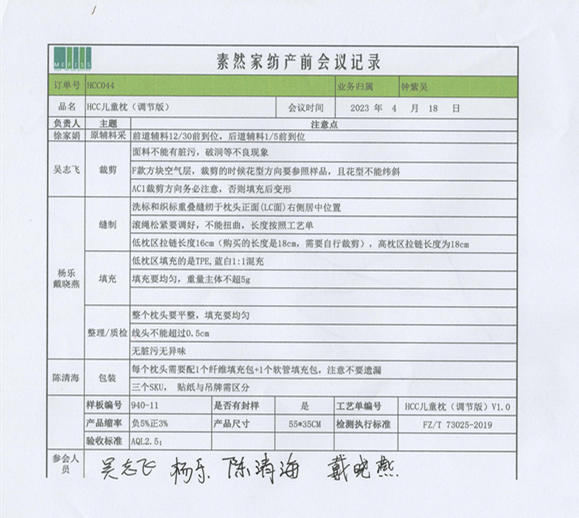
6. Routine Inspections During Production
Daily inspections during production are key to catching issues early. Mefiss’s quality control team conducts random checks throughout the production process, identifying and addressing any problems immediately. This real-time feedback helps maintain consistency and ensures that the final product meets our high standards.
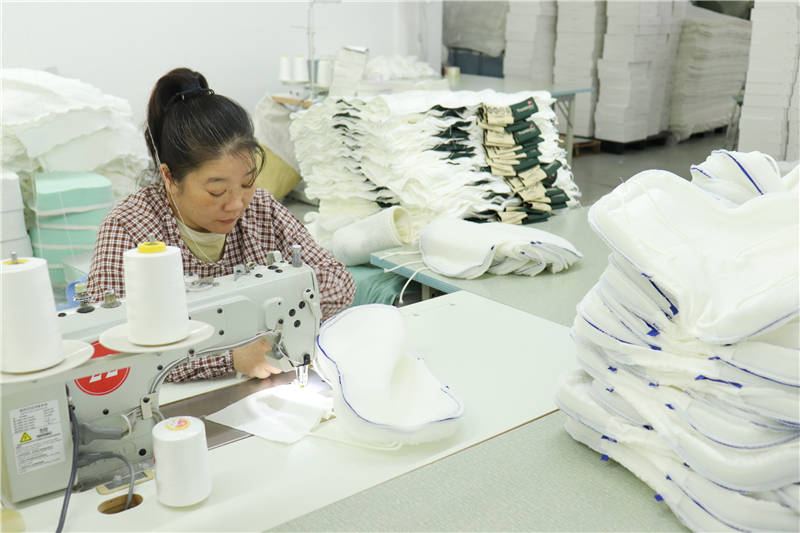
7. Double Quality Inspections for Finished Products
Final product inspection is the last line of defense in quality management. To minimize post-sale issues, Mefiss employs a double-inspection process, where two independent groups of inspectors check the finished goods before they are packed. This two-step inspection system significantly reduces the chances of defective products reaching the customer.
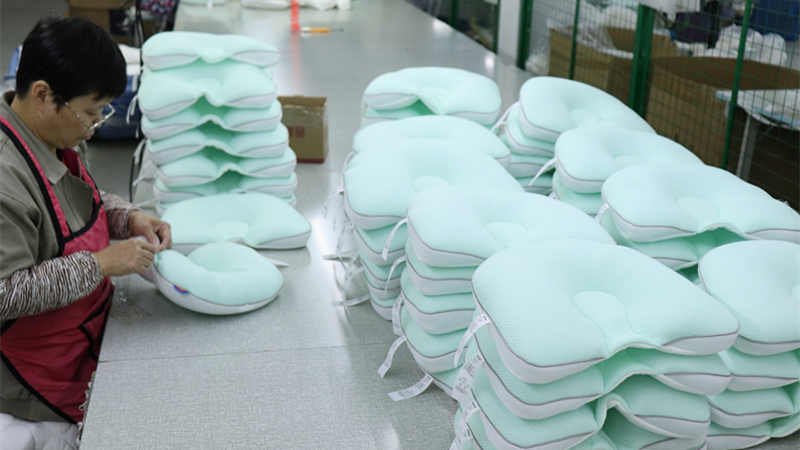
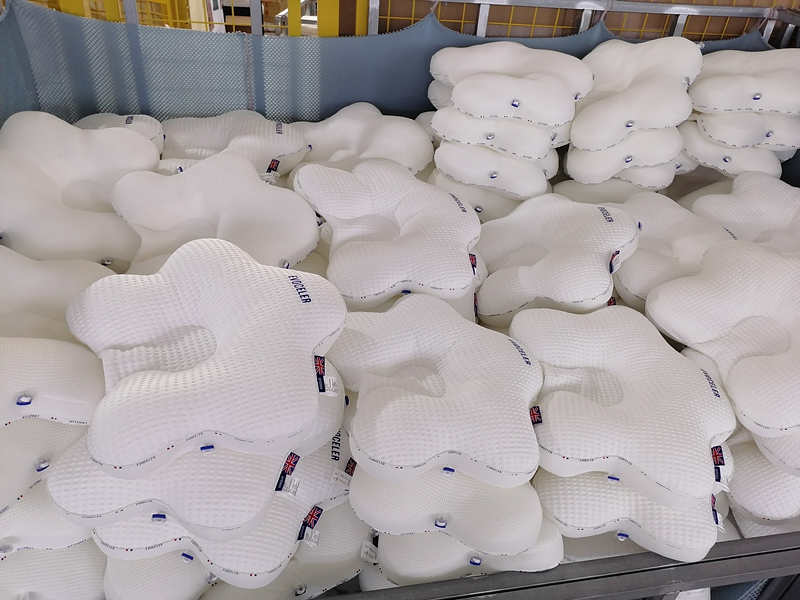
8. Metal Detection for Safety
Foreign metal contamination can pose a safety risk to consumers, which is why every finished product at Mefiss undergoes metal detection. Our metal detection machines are tested and calibrated for accuracy before each use, with records kept to ensure compliance. This extra step significantly reduces the risk of metal contamination, enhancing product safety.
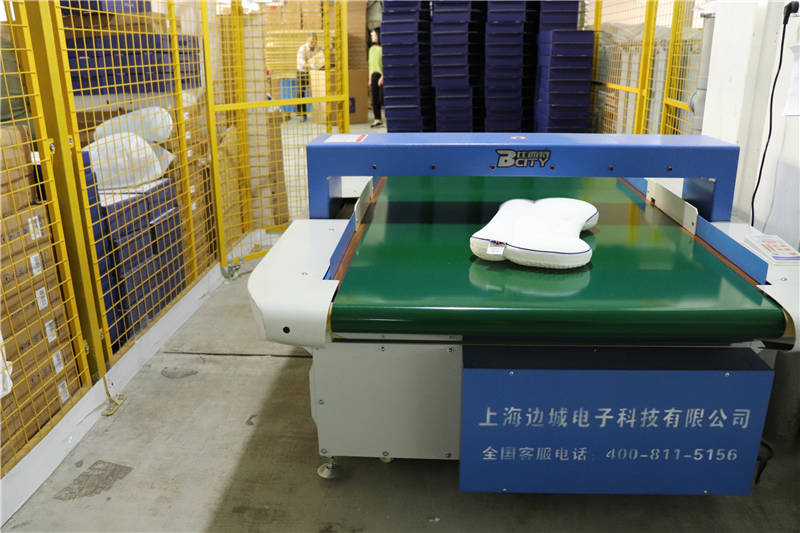
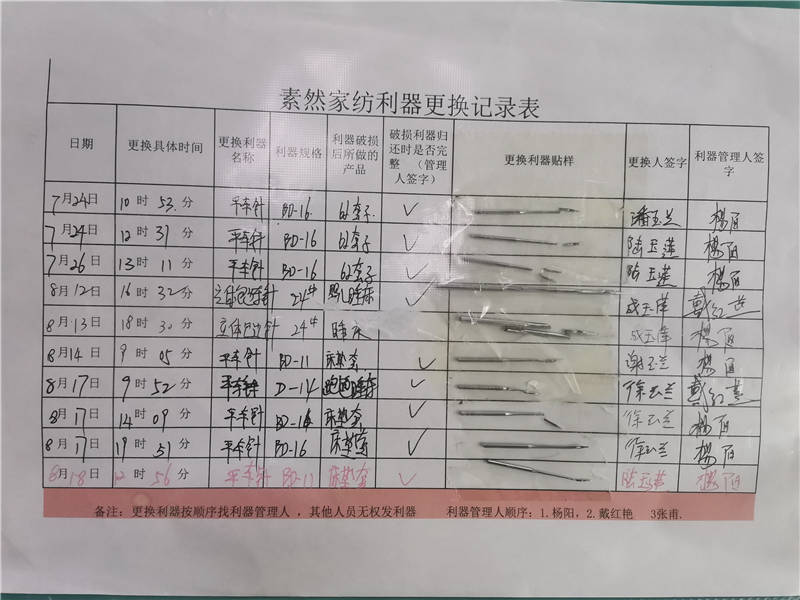
9. Strict Packaging Protocols
The packaging stage is another critical component of quality management. At Mefiss, packaging workers wear masks and hats, and unauthorized personnel are restricted from entering the packaging area to prevent contamination. All products are packed in moisture-proof bags and durable kraft paper boxes to ensure they arrive at their destination undamaged.
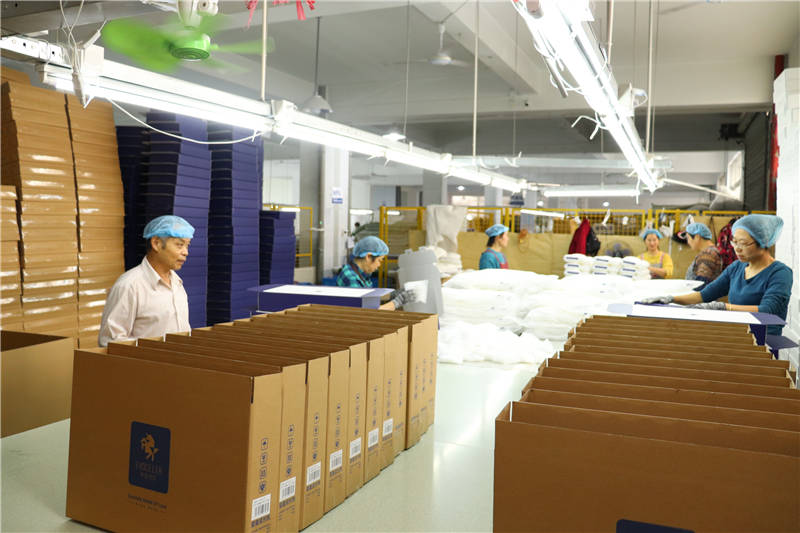
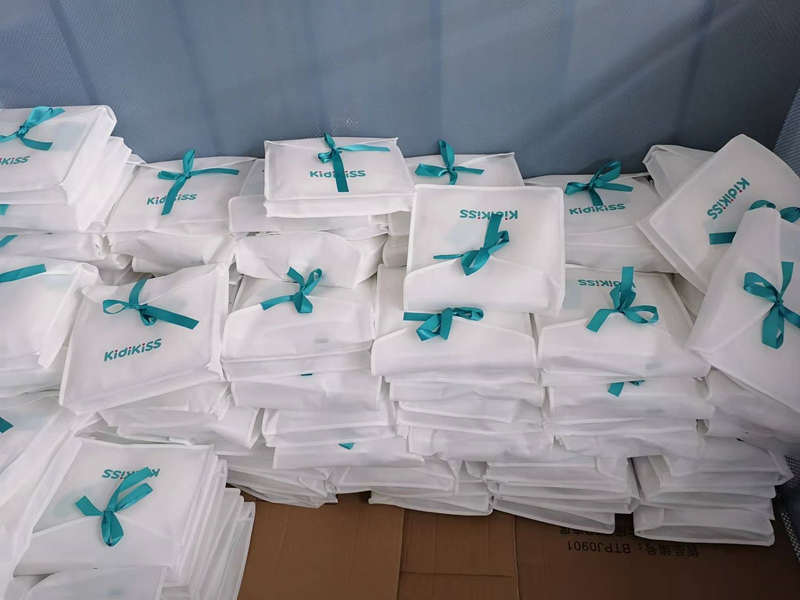
10. Warehouse and Shipping Management
Proper storage conditions are essential for maintaining product quality. Mefiss’s warehouse is designed with moisture-proof and fire-proof features, and finished products are stored according to shipping schedules. Before shipment, we inspect the transportation vehicle for damage, water accumulation, or dirt. Only after ensuring the vehicle is clean and safe do we load the products. Each step is carefully managed to ensure customers receive their goods in perfect condition.
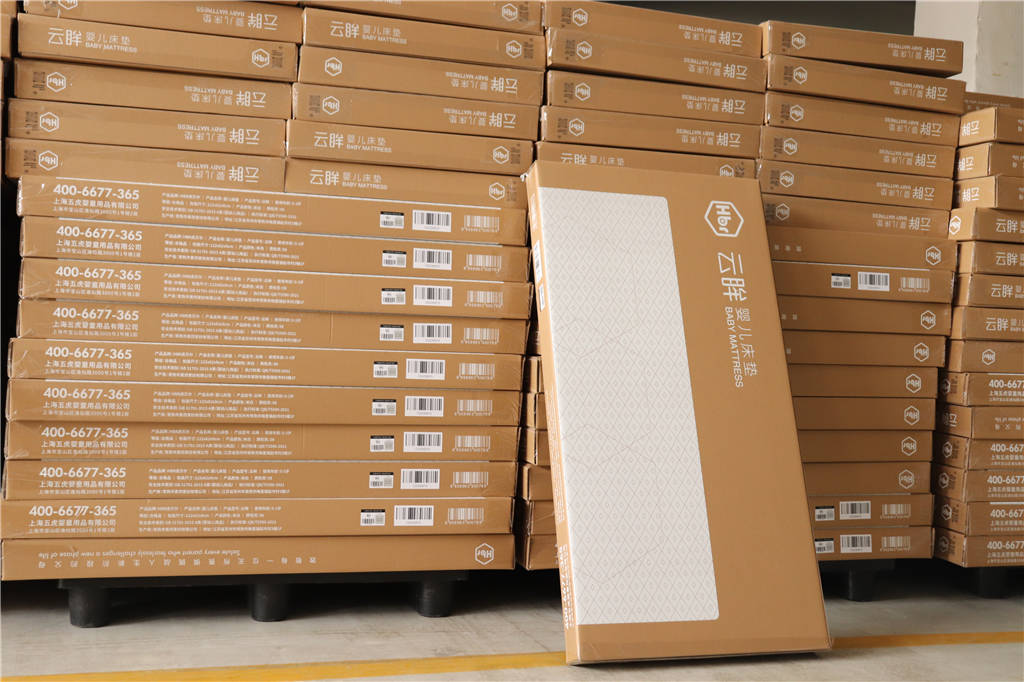
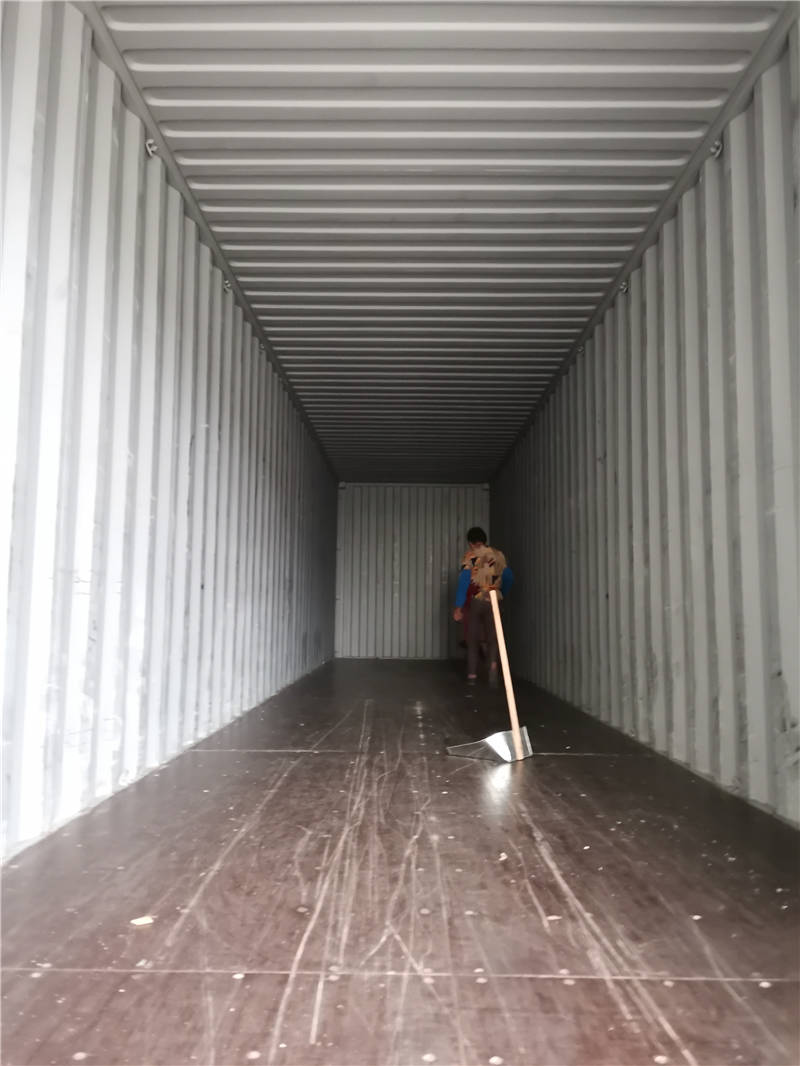
Conclusion
In the textile industry, quality management covers every stage of the production process. From raw material sourcing to final product shipment, Mefiss employs a series of stringent processes and standards to ensure that every item we produce meets the highest quality standards. It is this attention to detail and rigorous process control that allows us to consistently deliver superior home textile products to customers around the world.